Seals: Innovative solutions through cross-innovation
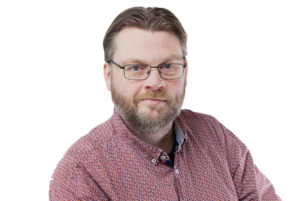
How can we prevent leaks? This is a question that valve manufacturers and users face every day. In this Armaturen Welt interview, Martijn Torenbeek from the PCV Group in Enschede, the Netherlands, presents some solutions for particular challenges.
These are all based on a "cross-innovation" approach, which involves the transfer of solutions from one industry to another. The company established itself as a specialist in sealing by developing the Flexring for Georg Fischer Piping Systems.
Leakage has been a problem for as long as valves have been around. How can we prevent leaks?
To put it simply, seals are a weak point. Hence our motto: the fewer seals, the fewer leaks. That is why in our projects we are always trying to keep the number of seals needed to a minimum. We can do this by changing the design, using alternative materials, or adding new functions.
Can you give us a specific example?
While testing a tap system we developed for a large brewery, it proved difficult to keep the CO2 system under pressure for two weeks. The gas supply system, which included a reduction system with safety-related functions, had ten seals. We modified the design so that only four were needed. We also took advantage of an existing but unused function – the tank had a tap with a rest position, but this was not being used. By incorporating this rest position, the pressure on the seals was reduced.
As the project progressed, we encountered another problem: the outer wall was made of cast aluminium, which proved to be porous. This meant that gas was able to escape through the outer skin. Therefore, we recommended that the client have the material for critical components produced by machining and not by casting techniques.
These challenges, which we solved on a small scale here, are also found for large tanks in the pharmaceutical, chemical or food industries. The basic principles can be transferred easily.
But do different fluids require different approaches?
Yes, definitely. Another example would be a can of lubricant which is used, among other things, in the engine rooms of ships.
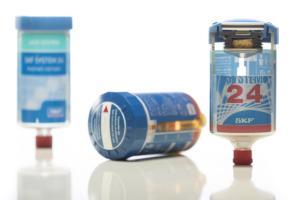
The required pressure in the can is provided by hydrogen, with even
minimal leakage limiting the service life and dosing accuracy. In addition, the pressure often dropped too quickly due to leakage – but the can is actually meant to be usable for twelve months. Here, too, we managed to
significantly reduce the number of seals and their length. We also opted for dynamic sealing solutions that are characterised by constant friction. The can design also had to ensure exact dosing, be easy to exchange, and work properly at temperatures from below zero to 50 degrees Celsius.
How did you solve these problems?
We applied our experience from a project with a pump system for liquid detergents. Here, too, smooth-running polymeric seals were used because elastomers, such as O-rings, cause too much friction and tolerance sensitivity and raise costs. We also completely redesigned the entire system and significantly reduced the number of seals.
How long does this kind of project take?
That project took us a total of two and a half years from the first brainstorming sessions, through the redesigns, to the start of mass production. The testing took a long time. After all, we had to ensure its accuracy as well as its ability to operate in a very wide temperature range.
Cleaning also poses another problem...
Yes, especially in the food industry. For example, one modern coffee machine with a milk frothing system actually had to be completely disassembled every time it needed to be cleaned. This can quickly turn into a puzzle with many pieces. Keeping things clean is an issue, especially when it comes to milk froth. So, we have also adapted the design of the milk frother for the manufacturer of this model of coffee machine. Previously, there was a narrow channel with a total of six O-ring and rubber seals. We split the channel into two halves. This meant that the machine could be easily taken apart at the critical point. The channels can be cleaned separately and easily reassembled. That's how we managed to solve the problem of seals and cleaning. And this principle can of course also be implemented on a large scale in the flow control industry.
Another example is a supplier of frozen soups and smoothies. There is a special machine to prepare the contents of the containers. In the cover of the soup packaging system, there is a blade that automatically chops the ingredients into small pieces. The challenge here was to find leak-free seals that are suitable for food use and recyclable. In addition, the spinning blade could not sit too close to the plastic seal, otherwise we would have to change the seal for a welded seam. Therefore, we fitted a labyrinth seal. With just one simple movement, the closure is at the right height and the food preparation can be started.
You have been working with seals for a long time, and developed a classic solution for pipelines...
Yes, the Flexring. It can be used for gas, water and sewage pipelines, and for pipes made of different materials or with different diameters. In the past, if a pipeline or fitting needed to be repaired, the replacement part always had to be made by hand. That was expensive and time-consuming. We developed our solution, the Flexring, on behalf of Georg Fischer Piping Systems in the late 1980s. It was a revolution in the industry. The Flexring consists of injection-moulded parts that interlock when they are pushed together, changing the shape of the ring. It is a self-reinforcing system, which means that this sealing ring can be used for fittings of different diameters. Of course, there have been a whole series of further improvements, but the basic principle remains the same.