Product development processes with savings potential
The aim of the PCV Group is clearly stated: the abbreviation in the company’s name stands for “People Creating Value”. A team of 40 engineers, scientists and administrators who, supported by other experts from a variety of disciplines when necessary, develop and optimise new products – also in terms of the associated production costs. These “nerds”, who are based in Enschede in the Netherlands, possess valuable know-how that has, so far, been used mainly by multinational companies in the household appliances, medical technology and industrial sectors. In this interview, Leo Giesen, a mechanical engineer by training, a Design for Six Sigma (DFSS) Black Belt, and a consultant with the PCV Group, offers some insights.
Mr Giesen, what is your role with the PCV Group?
I play a rather flexible role in our organisation. My most important task is to advise companies as they kick-off new projects. The actual implementation phase is then increasingly taken over by other colleagues. I am also a member of our quality-assurance team.
The main reason to call in the PCV Group is not always to reduce costs, but you and your colleagues often manage to achieve this. How do you manage that?
One actually always has to keep an eye on production costs, which is a strong element of the development process. We continuously ask ourselves how to achieve the highest possible added value at the lowest possible cost. The motto here is “high-tech meets low-cost”. In this way, significant value is added.
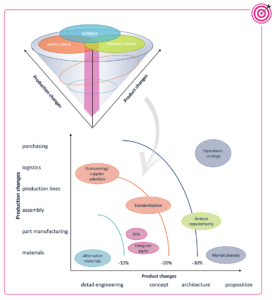
Can calling in external support save more costs than handling everything internally?
In my experience, yes, certainly. Naturally, I’m best placed to speak for the PCV Group. We take a more integrated approach to a product than the manufacturer themselves – from front end through to market maturity. We are also not as close to the product, which can be beneficial. Our work is wide-ranging both in terms of industry sector and application. On this basis, we use highly efficient cross-innovation effects, meaning that insights gained from other projects are transferred to similar challenges in other contexts. The laws of physics are universal. Additionally, we work pragmatically, which starts with us being in the position to create integrated teams made up of members who can contribute precisely those skills a given project requires.
In summary, we bring expertise and a special way of working that sets us apart from our clients – mainly large companies. Our workflow is characterised by structured creativity, and our contribution is perfectly integrated with our clients’ skills and knowledge. As a result, we can achieve higher standards, especially in terms of cost reduction.
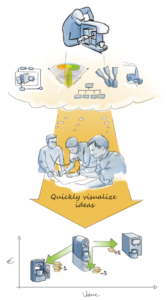
What exactly does “structured creativity” mean?
We adapt our procedures to the challenge at hand, while following a clear plan. Above all, structured creativity implies exploring the less obvious paths and doing so in a quicker and more target-oriented manner: namely, by using common insights gained from different perspectives and other development projects, which also leads to surprising results. As product developers, we usually take a top-down approach. However, a bottom-up approach can also prove to be useful if a certain project calls for it.
Is there a correlation between the level of investment during the product development process and low production costs?
Yes, a very clear one. One simple rule can be applied here: if you want to save, you have to invest more. The more care you take at the start of a development process, the less adaptations are required in later phases. Each subsequent change made to a product simply costs money.
Is a reduction in production cost necessarily associated with a drop in the quality of a product?
No, there is no clear link. A product manufactured in a cost-effective way can even be better than one produced more expensively under similar conditions.
Could you name a few examples of successful cost saving?
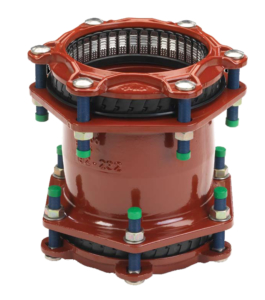
For one client, we were working on a connector for gas and water pipelines. This involved further improving an established market product while simultaneously saving costs in order to achieve an optimal balance between function – connection and sealing – and cost. We managed to do this by, among other things, reducing the number of components, developing a new element for all pipe materials and minimising the use of plastics and rubber. The cost was reduced by up to 35 per cent and the return on investment was achieved in less than a year. As a result, the market volume increased by 10 per cent, thanks to the improved quality and higher performance of the product.
Another example would be the spray heads found on bottles of household detergent in supermarkets. One could assume the development of such a standard, mass-produced product had been exhausted; however, were we able to reduce parts, produce the pump mechanism entirely out of plastic and reduce the total volume of plastic used. Every gram counts here. Due to the high production volume, the savings are enormous. Also, from a sustainability point of view, it saves resources. As a result of the improved product characteristics, our client benefited from an increase in market volume of 30 per cent.
In which fields is the pressure on costs particularly high?
As a rule of thumb, the most important thing for a new product is to enter the market quickly. The cost pressure here is not that significant yet. The longer they are on the market, the more pressure there is on costs. Therefore, new products possess the highest potential in terms of cost reduction.
Are there any trends in the area of product cost reduction?
Cost reduction is constantly increasing in importance. Product lifespans are becoming shorter, and global competition more fierce. Product are copied more and more readily.|
From a development point of view, what should companies really take to heart when wanting to save money?
One definitely has to bring all uncertainties clearly to the forefront and then focus on the particularly big ones. There is nothing worse than discovering at a later stage that unfounded decisions were taken earlier in the development process. Thoroughness is a fundamentally important and deciding factor. Corrections made at a later stage often prove to be expensive. Thus, it does not make a lot of sense to cut costs at the beginning of a project – that is definitely not the right time!